切削加工過程的在線監測與自適應控制
2013年08月23日 09:12點擊:3892作者:默認來源:>>進入該公司展臺
【中國機床商務網】導讀:數控加工技術是航空*制造技術的重要組成部分。隨著航空工業的不斷發展,航空制造業對數控加工技術的要求越來越高。而數控加工技術仍然存在著技術風險與問題,這種風險來自整個加工過程,如設備因素、人為因素、工件因素和刀具因素等。在實際的生產過程中,多軸數控加工過程并非一直處于理想狀態。切削力會導致彈性讓刀變形,殘余應力會引起工件的扭曲變形,機床振動、刀具磨損、切削熱等多種因素也會導致不同程度的加工變形。這就使得加工出來的零件和理論模型之間存在一定的偏差。在加工過程中一旦工藝參數選擇不合理,就會導致工件加工表面質量差、設備加工能力得不到充分發揮,同時機床組件及刀具的使用壽命也會受到嚴重影響。
在實際加工過程中,采用傳統加工技術選用的加工參數一般過于保守,且無法根據產品實際的加工狀態進行加工過程的優化。隨著*監控技術與測試手段的不斷發展,借助*傳感技術、數據處理技術與控制技術等進行復雜數控加工全過程幾何信息、物理信息獲取、處理,進而發展出加工狀態自動判定與優化的智能技術。這類技術一方面集成了車間長期的工程經驗,另一方面集成了通過科學分析得到的理論模型,通過兩者的結合對實時加工狀態進行判斷,根據實時工況進行工藝參數的自適應優化,實現連續、穩定、自動的控制加工過程并使其保持*狀態,進而獲得更高的加工精度和生產效率,從而實現加工過程控制從依賴技藝向依靠科學的方向發展。
關鍵技術
面向切削加工過程的自適應控制技術需要采用在線或在位的方式對加工過程中的切削力、主軸扭矩、工藝系統振動及刀具磨損等進行實時監測、動態分析、工藝參數優化以及反饋控制。因此,自適應控制技術的實現需要多種技術的支持,包括傳感器技術、信號處理技術、基于多傳感器信息融合技術、控制決策技術、數據庫技術等,其關系如圖1所示。
1傳感器技術
為了使系統能夠在復雜環境中、在無人干預的條件下正常工作,就必須使系統具有類似于人類的信息處理能力,即智能決策。而智能決策需要通過實時監測加工過程來獲得信息。在線監測直接面向加工過程,與具體設備和儀器相。因此,適用于加工過程的具有高實時性、高精度和高可靠性的傳感器是在線監測的關鍵。用于加工過程監測的傳感器主要有:功率傳感器、力傳感器、扭矩傳感器、聲發射傳感器、振動傳感器、攝像頭和激光。
(1)功率傳感器。
加工過程中的機床主軸或者驅動電機的功率可以通過功率傳感器獲得,根據監測到的功率數據,可對功率變化中出現的起伏、波紋、尖峰及短時下降進行判斷和預測,從而通過相關算法對功率曲線做平滑處理。此外,主軸有效功率可以表征刀具的切削力,根據切削力與主軸功率的關系,可將實時監測到的主軸功率轉換為刀具的切削力,從而獲得切削力的實時數據。
?。?)力傳感器。
為實現對切削加工過程的可靠監視,需要對金屬切屑分離過程所產生的力進行地測量和分析,從而識別出切削過程中出現的缺陷,如刀具磨損或斷裂,以及加工工件的損傷。切削力的測量可以采用直接法或間接法測量。在直接測量方法中,傳感器安裝在力的通道中,測量全部力,測量非常準確,與力的作用點無關;在間接測量方法中,部分力通過旁路傳遞,由于只有部分力作用在傳感器上,間接測力系統安裝后需要標定,系統的靈敏度與力的作用點有關。
(3)扭矩傳感器。
相對于有效功率,主軸扭矩能夠更準確地表征刀具的切削力。直接測量機床主軸的扭矩可以獲得更的切削力。鉆孔、攻絲和多主軸加工過程的監測使用測量主軸扭矩的方法來獲得切削力尤為有效。在多主軸加工過程中,每一個主軸上的切削過程所消耗的功率都比總的功率小得多,因此,在這種情況下就不能用有效功率來表征切削力,而是通過主軸扭矩來表征切削力。
(4)聲發射傳感器。
在切削過程中當刀具斷裂時,會產生聲發射信號。聲發射傳感器能監測到在切削過程中產生的聲發射信號,通過分析監測到的信號可以獲得刀具的信息。聲發射傳感器對監測小鉆頭和絲錐的破損尤為有效。在加工過程中傳感器可以監測到非常小的聲發射信號,再與有效功率或者主軸扭矩相結合,能夠可靠地監測到刀具的破損。尤其是在大型機床中監測非常小的刀具以及多主軸加工過程中,更能突顯出聲發射傳感器的優勢。
(5)振動傳感器。
在切削過程中掉刀、刀具破壞、機械碰撞等會產生異常的振動。振動傳感器可以監測切削過程中機床結構產生的振動,通過分析振動可以監測到掉刀、刀具破壞、工件超差、機械碰撞和嚴重的過程故障。振動傳感器也可以監測機床主軸的振動,為加工過程中的振動預測與控制提供數據。
(6)攝像頭。
在多主軸加工過程中,分別監測每個主軸成本比較高。這種情況下,可以采用攝像頭監測全部主軸。攝像頭可以監測20個或更多不同的主軸。在多鉆頭加工中攝像頭可以監測每一個鉆頭的掉刀和破損。監測系統在學習的時候,記錄并存儲多鉆頭的圖像,在監測過程中通過比較輪廓來監測每一個鉆頭。當光學識別系統性能優于基于其他傳感器的系統時,它可以用于更多的過程監測,例如檢查工裝,位置,完整性等。
?。?)激光。
當切削刀具過于細小時,出現異常情況引起的波動比較小,使用功率傳感器、力傳感器無法監測,或者沒有合適的位置安裝聲發射傳感器時,可以使用激光光柵。激光光柵可以提供一套可靠的刀具掉刀和破損監測方案。激光光柵也可以監測機床熱變形,例如監測加工中心主軸的長度變形。激光的另一個應用是,通過分析工件的反射光監測工件的粗糙度、顫振、切削的波紋等。
2信號處理
傳感器在加工現場采集到的模擬信號是不能被監測系統直接使用的,需要轉化為數字信號進而轉換為有實際意義的物理量。轉換過程一般包括轉換、放大、濾波、平滑等,這個轉換過程需要信號處理的。一般力、聲發射和振動傳感器都是壓電型傳感器,需要前置放大器把傳感器的電荷信號轉換成成正比例的電壓信號。聲發射放大器從傳感器獲得原始信號,并提供信號的學習條件、分析方法來增強聲發射監測。通過使用放大、過濾和均方根平均,將原始聲發射信號轉換成有價值的聲發射信號,可以在較低的頻率下可視化和監測。此外,振動放大器可配備過濾器和均方根轉換器,可以過濾掉無意義的噪聲獲得振動信息。監測系統常用的解決方案是使用單獨的為特定類型傳感器設計的信號調理放大器。信號調理器封裝在一個密閉的盒子里,連接電纜用編織鋼網屏蔽保護,這樣可以保證他們的抗振動和電氣隔離的特性。因此,傳感器、連接電纜和調理器可以在惡劣的加工環境下工作。
3基于多傳感器的信息融合
由于加工過程中切削條件和切削狀態的多樣性,導致對切削過程進行準確監控非常困難。傳統的基于單一傳感器的測量和分析往往難以保證識別精度。為了能夠更準確地獲得加工過程的狀態信息,需要使用多個相同或不同的傳感器從不同的方面進行測量。利用不同傳感器測量和輸出信息的互補性,采用多傳感器集成和信息融合技術,將描述同一個加工系統的多個物理量整合成系統的狀態向量,為系統的分析與診斷提供更全面的信息,使監測結果更加真實、可靠。
zui簡潔的多傳感器信息融合方法是,將每個傳感器的測量數據單獨輸入到融合系統中,如果每個傳感器所提供的信息反映的是環境中*不同的方面,那么可以將每個傳感器提供的信息直接轉換為加工系統狀態向量的不同分量。該方法的主要優點是融合算法簡單,運算量小。如果傳感器所提供的環境信息出現重疊,以及可能出現信息的冗余、矛盾和相關,甚至出現其中的某個傳感器影響其他傳感器的工作,則來自不同傳感器的信息就必須在多種表達層次上進行融合,zui終獲得加工系統的狀態向量。在這種情況下,多傳感器信息融合能獲得更的狀態信息。多傳感器信息融合主要有以下幾個方面的優點:提高了信息的可信度、增加了系統狀態向量的維數、提高了系統的容錯能力。
4控制決策
控制系統獲得了加工系統的狀態信息之后,綜合分析加工過程中監測到的數據,獲取加工過程中的振動、切削力、切削溫度、刀具磨損、加工變形等數據,與理想的加工狀態對比。將實際狀態和理想狀態信息交給內部專家系統處理,專家系統的推理機讀取知識庫中的經驗數據和加工系統自身的信息,分析加工系統的狀態信息來判斷加工系統的運行狀態是否理想。根據加工系統運行狀態及切削參數與加工過程振動、變形等因素之間的關系選取優化規則,動態優化工藝參數使加工系統達到更優的運行狀態。通過控制器硬件與機床NC系統之間的接口實現對機床主軸轉速、進給速度等切削參數的優化控制。專家系統的原理如圖2所示。
5數據庫技術
基于數據庫技術的工藝參數庫主要包括機床、刀具、工件材料、冷卻潤滑、加工匹配、零件特征、切削參數、運行狀態等信息,其中機床、刀具、工件材料、冷卻潤滑、加工匹配、零件特征給出了工藝系統的基本信息,切削參數、運行狀態描述了工藝系統在不同工藝參數下的運行狀態信息。工藝參數庫是工程實踐中長期積累的經驗數據,具有實際應用價值,可以為專家系統的決策提供工程經驗。
專家系統將機床、刀具、工件材料、冷卻潤滑、加工匹配、零件特征等工藝系統信息與切削參數、運行狀態的匹配關系作為參數優化的規則,以工藝系統當前的運行狀態為基本事實,依據加工過程理論模型及工藝參數庫中的經驗數據進行演繹推理,zui終得到系統當前的優化參數。專家系統推理機的數據庫系統如圖3所示。
已有產品及應用現狀
近年來,國內外針對加工過程的監測與自適應控制技術在航空發動機制造中的應用開展了不同層次的研究工作,典型的商用系統包括OMATIVE自適應控制系統、ARTIS刀具和處理監控系統、BRANKAMP-CNC集成刀具監控、MONTRONIX監控系統、NORDMANN刀具監測與過程控制系統等,這類監控系統所使用的主要傳感器如表1所示。
1OMATIVE自適應控制系統
OMATIVE自適應系統將自適應控制技術應用在數控機床上,在加工過程中根據切削力實時優化切削的進給速度,在保證刀具不受損壞的前提下提高加工效率。OMATIVE自適應系統主要功能:提高加工效率;保護刀具、機床、工件不受損害;實時監控、記錄切削加工狀況。刀具進給速度與切削厚度的關系如圖4所示。以色列OMATIVE公司做了大量工件切削對比實驗,OMATIVE自適應系統能夠大幅提高加工效率。OMATIVE自適應控制系統因其實用性*,現已被國外許多公司使用,如Siemens、Boeing和GeneralElectric等。國內航空航天、紡織、家電等行業的企業也陸續使用該產品。
2ARTIS刀具和處理監控系統
ARTIS刀具監控及機床狀況監控系統是由德國ARTIS公司研發的實時在線監控系統。在加工過程中,可準確地檢測到斷刀、鈍刀及掉刀狀況。一旦出現異常狀況,機床便立刻停機,避免刀具、工件及機床的再一次損傷。采用ARTIS的各種傳感器,可對加工及機床狀況進行監控。采用不同的監控方式還可有針對性地為用戶帶來更多益處,如采用ARTIS的自適應控制,不但可對刀具及機床狀況進行監控,同時還可以對加工周期進行優化,有效提高機床的加工效率。
3BRANKAMP-CNC集成刀具監控
BRANKAMP監控系統依據特定的監測限度保護設備,任何不規則力的形態都會馬上被監測出來,甚至是任何zui微小的誤差,在造成主要的傷害之前,這個監測系統立即發現并做出反應,如圖5所示。BRANKAMP監控系統為所有的金屬切割、沖壓、冷鍛等制造過程提供過程監測。BRANKAMP主要服務對象包括沖壓、冷成型加工、金屬切割等加工設備,主要應用于汽車制造行業、緊件加工行業、手機制造業、半導體加工行業、食品和飲料金屬包裝等行業領域。安裝BRANKAMP監測系統可以保護機械設備和昂貴模具,減少廢品和設備維修時間,節約成本,提高產品質量,同時具有在線監控以及可視化結果功能。
4MONTRONIX刀具和過程監控系統
MONTRONIX刀具和過程監控系統使用一個或多個壓力、扭矩、振動、功率傳感器和一個處理器,獲得實時的關于切削刀具、機床和加工過程的監控數據。該監控系統可以給制造系統的機床、刀具、工裝夾具、加工工件等提供保護,嚴格控制工件的加工質量,提高加工過程的安全和可靠性,減少加工成本。配套的可視化軟件(M-View)使得機器操作者能夠快速而地評估加工過程。其圖形化顯示包括:過程偏差,刀具損壞,逐漸增加的磨損量等,系統可以對這些信息進行記錄和評估。該系統可以在加工過程中的任何時候進行可視化顯示。
5NORDMANN刀具監測與過程控制系統
NORDMANN的解決方案可對加工過程中的刀具破損、磨損進行檢測,對碰撞干涉、刀具負載平衡狀態進行監控,從而對刀具和機床進行保護。此外,該系統還可以對工件的非正確裝卡狀態、錯誤的工件毛坯尺寸等進行檢測并在機床內對工件zui終形狀進行尺寸控制,從而保證產品的加工質量。在加工效率方面,NORDMANN監控系統可以通過間接方式對金屬切削過程中的有效功率、切削力等進行控制,從而可以減少空切時間、延長刀具使用壽命、zui大化進給與轉速以提高加工效率。NORDMANN監測系統可擴展下列額外的測量系統:力傳感器、聲發射傳感器、有功功率測量器、工件的有聲尺寸監測、光學激光傳感器、直接安裝于刀具切入部分的傳感器(圖6)。在監控過程中,該系統可以實時生成測量數據并顯示在PCU50/PCU70模塊的操作面板上,并可對刀具的磨損、破損等狀態進行評估。應用范圍上,NORDMANN監控系統可用于CNC車床、加工中心、磨床等設備加工過程中的功率、力、扭矩等物理量的監測與控制。
結束語
切削加工過程的在線監測與控制系統已在國外廣泛應用,并取得了顯著的效果。但是,這類系統在國內并未得到廣泛應用。隨著復雜結構產品的廣泛應用、產品服役性能對產品加工質量要求的不斷提升,以及生產企業對產品低成本率加工的不斷追求,采用相應的監控與優化系統對切削加工過程進行在線監控并進行切削參數的在線優化已逐漸成為智能加工技術研究與工程應用的重點,并將隨著數控加工技術以及復雜產品加工需求的發展而得到廣泛應用。
(文章來源:航空制造網)
在實際加工過程中,采用傳統加工技術選用的加工參數一般過于保守,且無法根據產品實際的加工狀態進行加工過程的優化。隨著*監控技術與測試手段的不斷發展,借助*傳感技術、數據處理技術與控制技術等進行復雜數控加工全過程幾何信息、物理信息獲取、處理,進而發展出加工狀態自動判定與優化的智能技術。這類技術一方面集成了車間長期的工程經驗,另一方面集成了通過科學分析得到的理論模型,通過兩者的結合對實時加工狀態進行判斷,根據實時工況進行工藝參數的自適應優化,實現連續、穩定、自動的控制加工過程并使其保持*狀態,進而獲得更高的加工精度和生產效率,從而實現加工過程控制從依賴技藝向依靠科學的方向發展。
關鍵技術
面向切削加工過程的自適應控制技術需要采用在線或在位的方式對加工過程中的切削力、主軸扭矩、工藝系統振動及刀具磨損等進行實時監測、動態分析、工藝參數優化以及反饋控制。因此,自適應控制技術的實現需要多種技術的支持,包括傳感器技術、信號處理技術、基于多傳感器信息融合技術、控制決策技術、數據庫技術等,其關系如圖1所示。

1傳感器技術
為了使系統能夠在復雜環境中、在無人干預的條件下正常工作,就必須使系統具有類似于人類的信息處理能力,即智能決策。而智能決策需要通過實時監測加工過程來獲得信息。在線監測直接面向加工過程,與具體設備和儀器相。因此,適用于加工過程的具有高實時性、高精度和高可靠性的傳感器是在線監測的關鍵。用于加工過程監測的傳感器主要有:功率傳感器、力傳感器、扭矩傳感器、聲發射傳感器、振動傳感器、攝像頭和激光。
(1)功率傳感器。
加工過程中的機床主軸或者驅動電機的功率可以通過功率傳感器獲得,根據監測到的功率數據,可對功率變化中出現的起伏、波紋、尖峰及短時下降進行判斷和預測,從而通過相關算法對功率曲線做平滑處理。此外,主軸有效功率可以表征刀具的切削力,根據切削力與主軸功率的關系,可將實時監測到的主軸功率轉換為刀具的切削力,從而獲得切削力的實時數據。
?。?)力傳感器。
為實現對切削加工過程的可靠監視,需要對金屬切屑分離過程所產生的力進行地測量和分析,從而識別出切削過程中出現的缺陷,如刀具磨損或斷裂,以及加工工件的損傷。切削力的測量可以采用直接法或間接法測量。在直接測量方法中,傳感器安裝在力的通道中,測量全部力,測量非常準確,與力的作用點無關;在間接測量方法中,部分力通過旁路傳遞,由于只有部分力作用在傳感器上,間接測力系統安裝后需要標定,系統的靈敏度與力的作用點有關。
(3)扭矩傳感器。
相對于有效功率,主軸扭矩能夠更準確地表征刀具的切削力。直接測量機床主軸的扭矩可以獲得更的切削力。鉆孔、攻絲和多主軸加工過程的監測使用測量主軸扭矩的方法來獲得切削力尤為有效。在多主軸加工過程中,每一個主軸上的切削過程所消耗的功率都比總的功率小得多,因此,在這種情況下就不能用有效功率來表征切削力,而是通過主軸扭矩來表征切削力。
(4)聲發射傳感器。
在切削過程中當刀具斷裂時,會產生聲發射信號。聲發射傳感器能監測到在切削過程中產生的聲發射信號,通過分析監測到的信號可以獲得刀具的信息。聲發射傳感器對監測小鉆頭和絲錐的破損尤為有效。在加工過程中傳感器可以監測到非常小的聲發射信號,再與有效功率或者主軸扭矩相結合,能夠可靠地監測到刀具的破損。尤其是在大型機床中監測非常小的刀具以及多主軸加工過程中,更能突顯出聲發射傳感器的優勢。
(5)振動傳感器。
在切削過程中掉刀、刀具破壞、機械碰撞等會產生異常的振動。振動傳感器可以監測切削過程中機床結構產生的振動,通過分析振動可以監測到掉刀、刀具破壞、工件超差、機械碰撞和嚴重的過程故障。振動傳感器也可以監測機床主軸的振動,為加工過程中的振動預測與控制提供數據。
(6)攝像頭。
在多主軸加工過程中,分別監測每個主軸成本比較高。這種情況下,可以采用攝像頭監測全部主軸。攝像頭可以監測20個或更多不同的主軸。在多鉆頭加工中攝像頭可以監測每一個鉆頭的掉刀和破損。監測系統在學習的時候,記錄并存儲多鉆頭的圖像,在監測過程中通過比較輪廓來監測每一個鉆頭。當光學識別系統性能優于基于其他傳感器的系統時,它可以用于更多的過程監測,例如檢查工裝,位置,完整性等。
?。?)激光。
當切削刀具過于細小時,出現異常情況引起的波動比較小,使用功率傳感器、力傳感器無法監測,或者沒有合適的位置安裝聲發射傳感器時,可以使用激光光柵。激光光柵可以提供一套可靠的刀具掉刀和破損監測方案。激光光柵也可以監測機床熱變形,例如監測加工中心主軸的長度變形。激光的另一個應用是,通過分析工件的反射光監測工件的粗糙度、顫振、切削的波紋等。
2信號處理
傳感器在加工現場采集到的模擬信號是不能被監測系統直接使用的,需要轉化為數字信號進而轉換為有實際意義的物理量。轉換過程一般包括轉換、放大、濾波、平滑等,這個轉換過程需要信號處理的。一般力、聲發射和振動傳感器都是壓電型傳感器,需要前置放大器把傳感器的電荷信號轉換成成正比例的電壓信號。聲發射放大器從傳感器獲得原始信號,并提供信號的學習條件、分析方法來增強聲發射監測。通過使用放大、過濾和均方根平均,將原始聲發射信號轉換成有價值的聲發射信號,可以在較低的頻率下可視化和監測。此外,振動放大器可配備過濾器和均方根轉換器,可以過濾掉無意義的噪聲獲得振動信息。監測系統常用的解決方案是使用單獨的為特定類型傳感器設計的信號調理放大器。信號調理器封裝在一個密閉的盒子里,連接電纜用編織鋼網屏蔽保護,這樣可以保證他們的抗振動和電氣隔離的特性。因此,傳感器、連接電纜和調理器可以在惡劣的加工環境下工作。
3基于多傳感器的信息融合
由于加工過程中切削條件和切削狀態的多樣性,導致對切削過程進行準確監控非常困難。傳統的基于單一傳感器的測量和分析往往難以保證識別精度。為了能夠更準確地獲得加工過程的狀態信息,需要使用多個相同或不同的傳感器從不同的方面進行測量。利用不同傳感器測量和輸出信息的互補性,采用多傳感器集成和信息融合技術,將描述同一個加工系統的多個物理量整合成系統的狀態向量,為系統的分析與診斷提供更全面的信息,使監測結果更加真實、可靠。
zui簡潔的多傳感器信息融合方法是,將每個傳感器的測量數據單獨輸入到融合系統中,如果每個傳感器所提供的信息反映的是環境中*不同的方面,那么可以將每個傳感器提供的信息直接轉換為加工系統狀態向量的不同分量。該方法的主要優點是融合算法簡單,運算量小。如果傳感器所提供的環境信息出現重疊,以及可能出現信息的冗余、矛盾和相關,甚至出現其中的某個傳感器影響其他傳感器的工作,則來自不同傳感器的信息就必須在多種表達層次上進行融合,zui終獲得加工系統的狀態向量。在這種情況下,多傳感器信息融合能獲得更的狀態信息。多傳感器信息融合主要有以下幾個方面的優點:提高了信息的可信度、增加了系統狀態向量的維數、提高了系統的容錯能力。
4控制決策
控制系統獲得了加工系統的狀態信息之后,綜合分析加工過程中監測到的數據,獲取加工過程中的振動、切削力、切削溫度、刀具磨損、加工變形等數據,與理想的加工狀態對比。將實際狀態和理想狀態信息交給內部專家系統處理,專家系統的推理機讀取知識庫中的經驗數據和加工系統自身的信息,分析加工系統的狀態信息來判斷加工系統的運行狀態是否理想。根據加工系統運行狀態及切削參數與加工過程振動、變形等因素之間的關系選取優化規則,動態優化工藝參數使加工系統達到更優的運行狀態。通過控制器硬件與機床NC系統之間的接口實現對機床主軸轉速、進給速度等切削參數的優化控制。專家系統的原理如圖2所示。
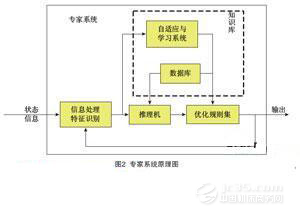
5數據庫技術
基于數據庫技術的工藝參數庫主要包括機床、刀具、工件材料、冷卻潤滑、加工匹配、零件特征、切削參數、運行狀態等信息,其中機床、刀具、工件材料、冷卻潤滑、加工匹配、零件特征給出了工藝系統的基本信息,切削參數、運行狀態描述了工藝系統在不同工藝參數下的運行狀態信息。工藝參數庫是工程實踐中長期積累的經驗數據,具有實際應用價值,可以為專家系統的決策提供工程經驗。
專家系統將機床、刀具、工件材料、冷卻潤滑、加工匹配、零件特征等工藝系統信息與切削參數、運行狀態的匹配關系作為參數優化的規則,以工藝系統當前的運行狀態為基本事實,依據加工過程理論模型及工藝參數庫中的經驗數據進行演繹推理,zui終得到系統當前的優化參數。專家系統推理機的數據庫系統如圖3所示。
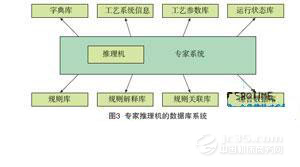
已有產品及應用現狀
近年來,國內外針對加工過程的監測與自適應控制技術在航空發動機制造中的應用開展了不同層次的研究工作,典型的商用系統包括OMATIVE自適應控制系統、ARTIS刀具和處理監控系統、BRANKAMP-CNC集成刀具監控、MONTRONIX監控系統、NORDMANN刀具監測與過程控制系統等,這類監控系統所使用的主要傳感器如表1所示。

1OMATIVE自適應控制系統
OMATIVE自適應系統將自適應控制技術應用在數控機床上,在加工過程中根據切削力實時優化切削的進給速度,在保證刀具不受損壞的前提下提高加工效率。OMATIVE自適應系統主要功能:提高加工效率;保護刀具、機床、工件不受損害;實時監控、記錄切削加工狀況。刀具進給速度與切削厚度的關系如圖4所示。以色列OMATIVE公司做了大量工件切削對比實驗,OMATIVE自適應系統能夠大幅提高加工效率。OMATIVE自適應控制系統因其實用性*,現已被國外許多公司使用,如Siemens、Boeing和GeneralElectric等。國內航空航天、紡織、家電等行業的企業也陸續使用該產品。

2ARTIS刀具和處理監控系統
ARTIS刀具監控及機床狀況監控系統是由德國ARTIS公司研發的實時在線監控系統。在加工過程中,可準確地檢測到斷刀、鈍刀及掉刀狀況。一旦出現異常狀況,機床便立刻停機,避免刀具、工件及機床的再一次損傷。采用ARTIS的各種傳感器,可對加工及機床狀況進行監控。采用不同的監控方式還可有針對性地為用戶帶來更多益處,如采用ARTIS的自適應控制,不但可對刀具及機床狀況進行監控,同時還可以對加工周期進行優化,有效提高機床的加工效率。
3BRANKAMP-CNC集成刀具監控
BRANKAMP監控系統依據特定的監測限度保護設備,任何不規則力的形態都會馬上被監測出來,甚至是任何zui微小的誤差,在造成主要的傷害之前,這個監測系統立即發現并做出反應,如圖5所示。BRANKAMP監控系統為所有的金屬切割、沖壓、冷鍛等制造過程提供過程監測。BRANKAMP主要服務對象包括沖壓、冷成型加工、金屬切割等加工設備,主要應用于汽車制造行業、緊件加工行業、手機制造業、半導體加工行業、食品和飲料金屬包裝等行業領域。安裝BRANKAMP監測系統可以保護機械設備和昂貴模具,減少廢品和設備維修時間,節約成本,提高產品質量,同時具有在線監控以及可視化結果功能。

4MONTRONIX刀具和過程監控系統
MONTRONIX刀具和過程監控系統使用一個或多個壓力、扭矩、振動、功率傳感器和一個處理器,獲得實時的關于切削刀具、機床和加工過程的監控數據。該監控系統可以給制造系統的機床、刀具、工裝夾具、加工工件等提供保護,嚴格控制工件的加工質量,提高加工過程的安全和可靠性,減少加工成本。配套的可視化軟件(M-View)使得機器操作者能夠快速而地評估加工過程。其圖形化顯示包括:過程偏差,刀具損壞,逐漸增加的磨損量等,系統可以對這些信息進行記錄和評估。該系統可以在加工過程中的任何時候進行可視化顯示。
5NORDMANN刀具監測與過程控制系統
NORDMANN的解決方案可對加工過程中的刀具破損、磨損進行檢測,對碰撞干涉、刀具負載平衡狀態進行監控,從而對刀具和機床進行保護。此外,該系統還可以對工件的非正確裝卡狀態、錯誤的工件毛坯尺寸等進行檢測并在機床內對工件zui終形狀進行尺寸控制,從而保證產品的加工質量。在加工效率方面,NORDMANN監控系統可以通過間接方式對金屬切削過程中的有效功率、切削力等進行控制,從而可以減少空切時間、延長刀具使用壽命、zui大化進給與轉速以提高加工效率。NORDMANN監測系統可擴展下列額外的測量系統:力傳感器、聲發射傳感器、有功功率測量器、工件的有聲尺寸監測、光學激光傳感器、直接安裝于刀具切入部分的傳感器(圖6)。在監控過程中,該系統可以實時生成測量數據并顯示在PCU50/PCU70模塊的操作面板上,并可對刀具的磨損、破損等狀態進行評估。應用范圍上,NORDMANN監控系統可用于CNC車床、加工中心、磨床等設備加工過程中的功率、力、扭矩等物理量的監測與控制。

結束語
切削加工過程的在線監測與控制系統已在國外廣泛應用,并取得了顯著的效果。但是,這類系統在國內并未得到廣泛應用。隨著復雜結構產品的廣泛應用、產品服役性能對產品加工質量要求的不斷提升,以及生產企業對產品低成本率加工的不斷追求,采用相應的監控與優化系統對切削加工過程進行在線監控并進行切削參數的在線優化已逐漸成為智能加工技術研究與工程應用的重點,并將隨著數控加工技術以及復雜產品加工需求的發展而得到廣泛應用。
(文章來源:航空制造網)
上一篇:柔性測量系統助力汽車動力總成制造
下一篇:焊接工具及焊原理
- 凡本網注明"來源:機床商務網"的所有作品,版權均屬于機床商務網,轉載請必須注明機床商務網,//www.wzmyfl.com/。違反者本網將追究相關法律責任。
- 企業發布的公司新聞、技術文章、資料下載等內容,如涉及侵權、違規遭投訴的,一律由發布企業自行承擔責任,本網有權刪除內容并追溯責任。
- 本網轉載并注明自其它來源的作品,目的在于傳遞更多信息,并不代表本網贊同其觀點或證實其內容的真實性,不承擔此類作品侵權行為的直接責任及連帶責任。其他媒體、網站或個人從本網轉載時,必須保留本網注明的作品來源,并自負版權等法律責任。
- 如涉及作品內容、版權等問題,請在作品發表之日起一周內與本網聯系,否則視為放棄相關權利。